Military platforms can stay in service for several decades, so ensuring that the electronic equipment onboard is fully functioning and carrying out its primary roles can be a significant challenge. While it may not grab the headlines, it is critical for militaries to plan for electronics obsolescence, including parts no longer being available, to ensure that mission critical equipment such as computers, do not go out of service when they are needed the most.
When it comes to buying a new computer or device, most of us are used to replacing our old tech every couple of years. We go to our local electronics shop or go online and simply buy a new product that meets our requirements.
We can sometimes make an old laptop or desktop computer work for longer, but that’s typically a stretch, and without any significant upgrades they start to run slow and don’t perform like they did when they were new.
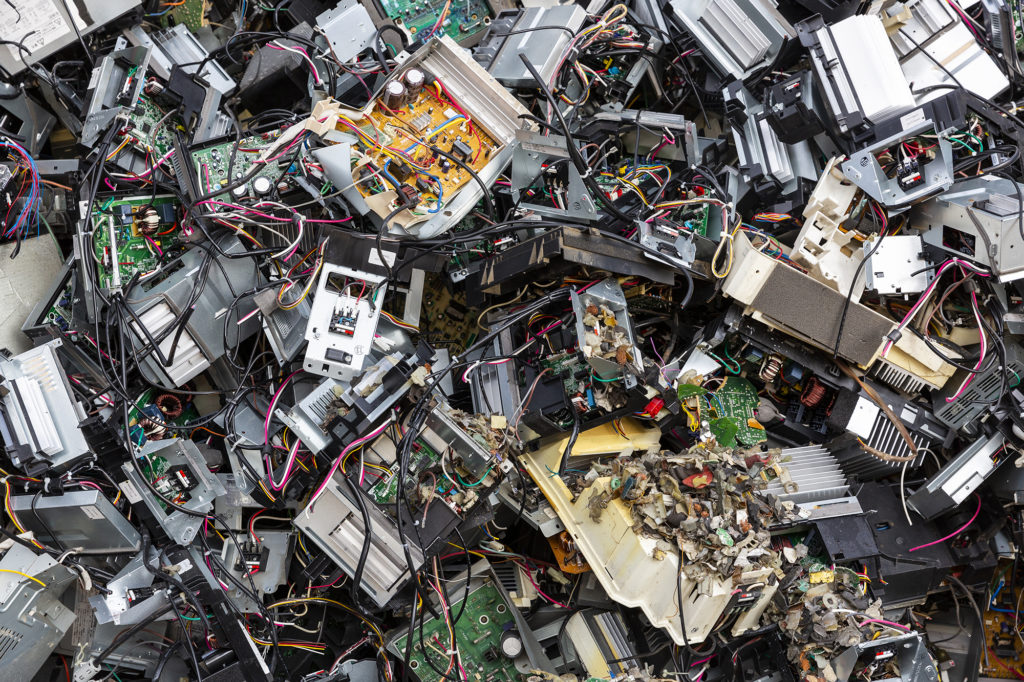
The complex military market
While it’s simple for individuals to replace their computers with a brand-new product, there’s a whole host of challenges in the defence world. In this complex market space, procurement cycles can span decades and equipment lifecycles can stretch to 20 or 30 years (if not more!), so it’s not as simple as just buying a new computer off the shelf every couple of years.
Another added complexity is that computers installed on ships, aircraft or vehicles normally have specific roles and functions – such as controlling a sensor, weapon or other systems onboard – with dedicated software to ensure that a soldier, sailor or aviator can operate it 24 hours a day.
It’s no understatement to say that computers play a critical part in modern military operations, so when a computer fails there needs to be a plan in place for its prompt repair or replacement, including sourcing and replacing components.
What is obsolescence management?
Obsolescence management in the electronics world is a complex undertaking, identifying and planning for when components and software will reach their end of life, and determining how to mitigate the risks associated with this.
Take for example a land vehicle that may have been in service for the last ten years. If a processor in one of the platform’s computers fails and this particular processor is no longer made by the original equipment manufacturer (OEM), a new part will have to be found.
That’s a big deal because not only do you have to source a new component and make sure that it works when integrated into the vehicle’s legacy system, but you also have to make sure the installed software is compatible with your new part, which could require new qualification of the system and sign off from the design authority.
What may have just been one part becoming obsolete could actually turn into a costly vehicle upgrade programme.
How to mitigate and de-risk for obsolescence
There are several strategies when it comes to obsolescence management and mitigating the risks involved.
One approach would be to buy and stock enough spare parts – such as processors, controllers and Printed Circuit Boards – so that you are covered for the remainder of the programme.
While this works in theory, and can work for smaller projects, it is simply too expensive to buy and store the number of parts needed to mitigate obsolescence over several decades of a defence programme.
A better strategy is to utilise industrial parts that are specifically designed to have a longer life, especially when compared to standard off-the-shelf commercial components. An example here is embedded processors, which are microprocessors that are designed specifically for the needs of an embedded system.
As we explain in more detail in this blog, embedded processors are intended to have an extremely long life and are required to be ‘always on’, meaning that it’s very rare that they are switched off, and performance must always be constant.
The GRiD approach to obsolescence
Here at GRiD, we ensure that we have ‘full configuration control’ over our military laptops and tablets, meaning we design the products and subcomponents – such as PCBs – so that a) they last for a decade and even longer, and b) we understand what components make up a product and can mitigate for obsolescence to a very detailed level.
With this kind of control, for example, we can recommend to our customers when it is an optimum time for a mid-life upgrade.
We also ensure flexibility in the design phase by including both legacy and modern interfaces in order to help alleviate any integration issues, and even with internal changes the computer itself will still fit in the same space that it was initially designed for. The use of connectors, such as the D38999, also allows us to standardise across products.
This adherence to the form-fit-function methodology once again gives us a head start when it comes to obsolescence.
Read more: Box-on, Box-off: GRiD’s cost-effective solution to vehicle computer upgrades
Our approach to obsolescence has never been more important. With the conflict in Ukraine and far-east factory shutdowns caused by Covid, obsolescence management has become a number one priority for the electronics industry. Component lead times are commonly over 12 months and, in some cases, companies have decided to end product lines where the supply chain challenges they face are too great to continue supplying product.
Thankfully, GRiD is in a fortunate position as we own the design and have in-depth knowledge of every component used. Where necessary, we can use like-for-like semiconductors and components (form, fit, function) or even re-design sub-components to overcome the supply challenges. Without our in-house design team, here in the UK, this would just not be possible.
Conclusions
Obsolescence management is a complex undertaking, but it is something we plan for from the initial design of our tablets and laptops.
Our deep understanding of all the components that are installed in a GRiD computer, including long-life components, allows us to optimise our obsolescence management, which ultimately benefits the customers and allows them to manage their inventory accordingly and plan ahead for future upgrades.
Want to learn more about best practices for obsolescence management? Contact us if you require further assistance and our expert team can advise on +44 (0)1628 810 230 or drop an email to sales@griduk.com